Smaller Medical Devices Mean Smaller Batteries
New battery designs are needed as new types of implantable medical devices emerge.
March 29, 2024
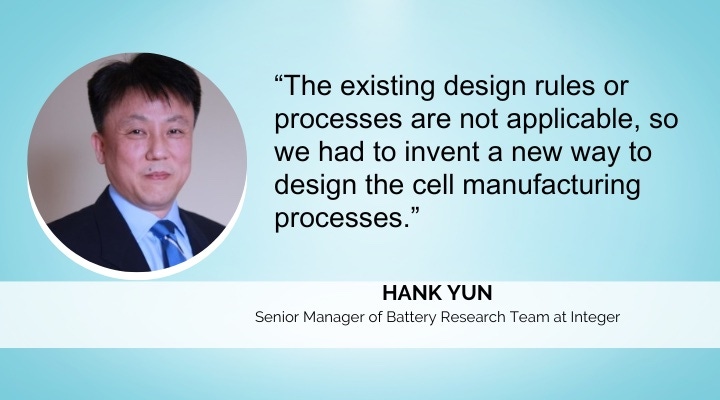
At a Glance
- Small-sized medical device sensors and monitors typically consume less power than therapeutic devices
- Integer is working on three different approaches to miniaturization for both primary and rechargeable cells
Contact lenses that might one day monitor eye health. Wearable devices that can go seven days without recharging. Pacemakers that can be implanted minimally invasively. All of these products are here (or at least maybe not so far off), and they will need a power source that can be made as small and long-lasting as possible. Design News spoke with Hank Yun, senior manager of battery research team at Integer, about what he thinks are some of the trends and developments in batteries for the medical implantable world.
Trends in Medical Device Implantables
“What we are seeing right now is that the market is moving toward more of a variety of implantable devices, from the very conventional, like a pacemaker, defibrillator, and neuromodulation, to an expanded area of applications such as more diagnostic ones,” said Yun. “Some of them are still sticking with therapy-based, but some of them are even beyond that, like sensors and monitors.”
He explained that these sensors and monitoring devices consume less power than typical therapeutic ones. “By the nature of it, it needs to be kind of small,” he said. “You don’t want to have a big surgery or incision [to implant] small monitoring devices or sensors.”
The trigger point in making batteries smaller is that there is less energy required for such applications, Yun said. “That's the starting point of the discussions for the smaller devices. That means the existing design rules or processes are not applicable, so we had to invent a new way to design the cell manufacturing processes,” he said.
There are two possible approaches to redesigning cells, Yun said. The first is sticking with the same chemistry as larger batteries but improving the development of the design processes. The second is to use completely different chemistries.
Yun’s team takes the former approach. “We would like to maintain our current electrochemistry as is and focus on the assembly processes and how we make the battery itself,” he said, noting that this is because of the unique circumstances of the medical device industry. “Once you have a battery solution for the medical device industry, it takes forever to become commercialized,” he explained. “It has to go through qualifications and validations, and then if you go to regulatory submissions, FDA will ask for real-time data. This is understandable because we’re talking about a patient’s life, so we have to be super conservative,” he said.
The commercial world does not have these regulations, Yun said. “For example, they are doing a thin-film battery,” he noted. “So many different players are working on it, and I think the market is going to easily accept this new concept without waiting three years for real-time data.”
Another issue is that batteries need to be sealed. “But in some cases, if there is a very tiny leak, that’s kind of acceptable [in the commercial world],” Yun said. The medical device industry requires zero leaks and is subject to very sophisticated helium leak detection in every single cell, he said. “So even though there is a good solution and a widely accepted technology on commercial electronic applications, we cannot use it as easily for medical,” Yun explained.
New Ideas for Miniaturization
Yun’s company, Integer, is working on three different approaches to miniaturization for both primary and rechargeable cells, he said.
The Xcellion MicroCoin offers a stack configuration with a biocompatible titanium enclosure that allows the battery to be in direct contact with the human body, and glass-to-metal seal. Its energy density is ~180Wh/L for M4190.
Integer’s Miniature Boat-Shape cell has a stack configuration, which offers expanded design flexibility. It also has a biocompatible titanium enclosure and a glass-to-metal seal and an energy density of ~180Wh/L for M4220.
“Another one we make is a miniature cylindrical cell, which is very tiny in diameter,” Yun said. It has a wound configuration, biocompatible titanium enclosure, glass-to-metal seal, and an energy density of ~160Wh/L for M4396.
All Integer’s miniaturized cells have similar seal reliability to conventional batteries, and the cylindrical form factors are well suited for implantation using less-invasive surgical tools.
“There are so many companies working on futuristic devices, in some cases for monitoring of some health index and some for even more adventurous things like AR or VR,” Yun concluded. “So that's why we need to make our battery two or three order of magnitude smaller. And that's really the key to the development. That's what we've been putting our effort into.”
About the Author(s)
You May Also Like