Why Simulation Is a Key Pillar of Industry 4.0
Simulating factory operations could reduce costs, speed up implementation, and reduce risks of failures and downtime.
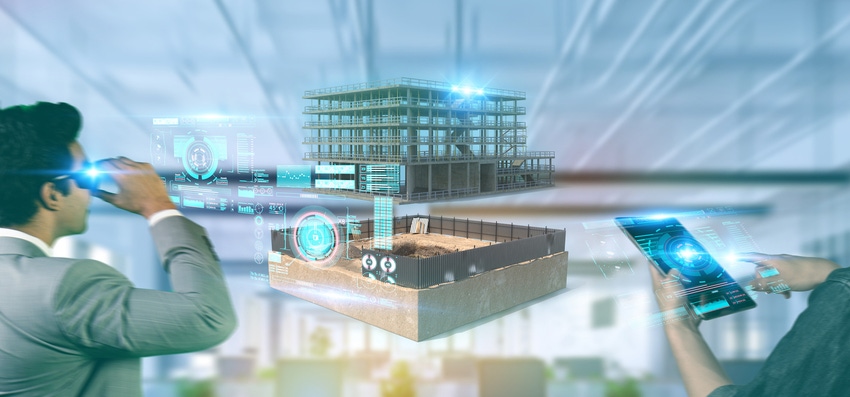
At a Glance
- Simulation can be used to understand workflow and resource requirements.
- Lead times, time-in-system, inventory, bottlenecks, scheduling, and more can be analyzed.
- Digital twins connect the virtual factory to actual operations.
We test drive cars before we buy them, focus-group new products before we sell them, and try our food before we serve it. So, when it comes to capital expenditure (CapEx) projects in manufacturing, why wouldn’t companies simulate how they work before making significant investments?
Some executives think spreadsheets and layout drawings are sufficient to understand the likely impacts of a major change. What they often don’t realize is that simulation, which provides a system-wide view of the effect of changes to the factory, can actually end up costing less, speed up implementation, greatly improve the new system, and reduce risks of failures and downtime. Simulations are also the first step toward building a “digital twin,” which combines simulation insights with real-time sensor data to build a dynamic digital replica of a physical system.
This is especially important today, as the push for digital transformation and optimization becomes a vital competitive advantage for manufacturers facing ongoing economic uncertainties, labor challenges, and supply chain issues. According to a study by McKinsey, Industry 4.0 solutions can deliver 30%-50% reductions in machine downtime, 10%-30% increases in throughput, and 15%-30% improvements in labor productivity.
Simulations can help manufacturers achieve these gains while minimizing risk. Below, I’ll unpack the key applications, benefits, and types of simulations, as well as some best practices for implementing them.
Simulation Applications & Benefits
Simulation allows manufacturers to develop and test new concepts, systems, operating policies, and resource policies before implementation—without disturbing their existing operations.
For instance, a client wanted to analyze the flow of materials from warehouse to assembly line to optimize the number of resources (e.g., forklifts and tuggers) required. A simulation model was created to understand the current process and operation. This was accomplished by tracking each part and then running various scenarios to deliver an optimized solution.
Simulation models—including videos, 3D designs, throughput data, utilization reports, and more—also helped lay the groundwork for a successful implementation in the case of another manufacturer. This manufacturer wanted to design a new test line with an optimal layout, streamlined process, and minimal material flow. Another client seeking to automate a manufacturing line using robots also benefited from simulation by validating how these machines impacted operations and performance.
What Exactly Can Be Simulated?
These are just a few of many applications, which can broadly be broken down into three categories:
The Need for and the Quantity of Equipment and Personnel
Whether it’s finding the ideal layout for your factory floor, understanding how and where to allocate your resources, or evaluating the impact of new equipment or a change in product mix (e.g., on labor requirements), simulations can provide the insights manufacturers need to make the right decisions in today’s competitive landscape.
Performance Evaluation
Making improvements starts with an in-depth understanding of what’s working and what’s not. Simulations can help run a number of different analyses to evaluate performance, from throughput and capacity utilization analyses to assessments of lead times, time-in-system, inventory, bottlenecks, and more.
Evaluation of Operational Procedures
Operational procedures are the lifeblood of a successful manufacturing facility—and simulations can ensure they’re working effectively. Production scheduling, materials policies, control strategies (e.g., for automated guide vehicles and conveyors), system reliability analyses, and just-in-time strategies are some of the procedures that simulation models can help improve.
In addition to overcoming the issues listed above, simulations can:
Increase throughput
Decrease time a part is in the system
Reduce in-process inventories of parts
Increase utilization of machines and workers
Increase on-time deliveries of products to customers
Reduce capital requirements or operating expenses
Ensure that a proposed system design will operate as expected
Reduce time to market
Minimize errors and debugging in the plant/shopfloor
Test new programs free of cost
Perform virtual commissioning
Create a digital twin
Popular Simulation Types
As technologies continue to develop and artificial intelligence (AI) tools gain momentum, simulations are evolving in kind. Three popular types that manufacturers should have on their radar include:
Discrete Event Simulation (DES)
DES models a sequential process, only analyzing events in which a change of state occurs. Take a production line: with DES, every task along the line is modeled according to when it arrives and departs. By breaking each task up into discrete events—i.e., arrival or departure—manufacturers can help visualize the movements needed to optimize output and adjust each event as needed.
The most common DES tool is Microsoft Excel, in which a DES model takes inputs, processes the inputs for a certain time period as per the system’s behavior, and produces outputs as results of the simulation analysis. However, a DES model can also interact with advanced database and industrial systems to fetch real-time data.
These efforts are particularly important today, when the lead time available to bring new products and services to market is shrinking. Even introducing one new variant increases the complexity of procurement, storage, processing, logistics, and more across the supply chain. That, in turn, can lead to uncertainty of deliverables and throughput. DES analysis can help.
Robotic Simulation
Customized robots used in manufacturing can cost up to $400,000 per system—so it’s important that manufacturers leverage them effectively.
Before making that investment, manufacturers can use robotic simulation to create a digital representation of a robot and test capabilities and performance—without having the physical robots in place. This reduces a production system's shutdown time and provides engineers with the flexibility to try different ideas and formulate scenarios in a digital environment.
Safety is critical when it comes to integrating robotics into operations. While automation can reduce workplace hazards, robots can also present danger to human workers, especially when they’re first introduced. Ergonomic robotic simulations can help manufacturers build in rules and detailed pathways to ensure no workers will collide with these tools, while optimizing cycle times for various functions—including pick-and-place, cutting, spot welding, arc welding, drilling, riveting, painting, and safety operations.
Emulation
Emulation helps create a “digital twin,” whereby the virtualization of a manufacturing system/factory floor is connected to the actual operations. In virtual commissioning, for instance, a virtual replica of a physical system is developed and establishes two-way communication with the control system.
Unilever was an early adopter of digital twin technology, creating digital models via sensor-equipped machines that could track conditions and test operational changes. As The Wall Street Journal reported, “The devices send real-time information on temperature, motor speed, and other production variables into the cloud. Algorithms take in the data and use advanced analytics to map out the best operational conditions. Workers on site track product quality with handheld devices, modeling solutions to problems and sharing data with colleagues in other locations.”
At just one of the company’s sites, the digital twin saved Unilever nearly $3 million in the first year.
Making Simulations a Reality
Deploying simulations successfully comes with its own set of considerations. Whether your company is performing a simulation yourself or engaging a partner to execute the work, here are three keys to success to keep in mind.
First, it’s important to have people with practical knowledge of the operational challenges workers face offering their counsel on the simulation side.
Second, comprehensive checklists customized to each simulation—including each aspect of a given process or operation—can ensure simulations run smoothly.
Finally, professionals should document their lessons learned once a simulation is complete; as technologies and processes continue to evolve at a rapid pace, these lessons can provide critical insights to future projects.
It’s more important than ever that manufacturers adopt new technologies and optimize their processes. Simulations can mitigate risks, cut down on implementation costs, and reduce delays—so that when a new machine, line or procedure is ready to go, your team will be, too.
About the Author(s)
You May Also Like